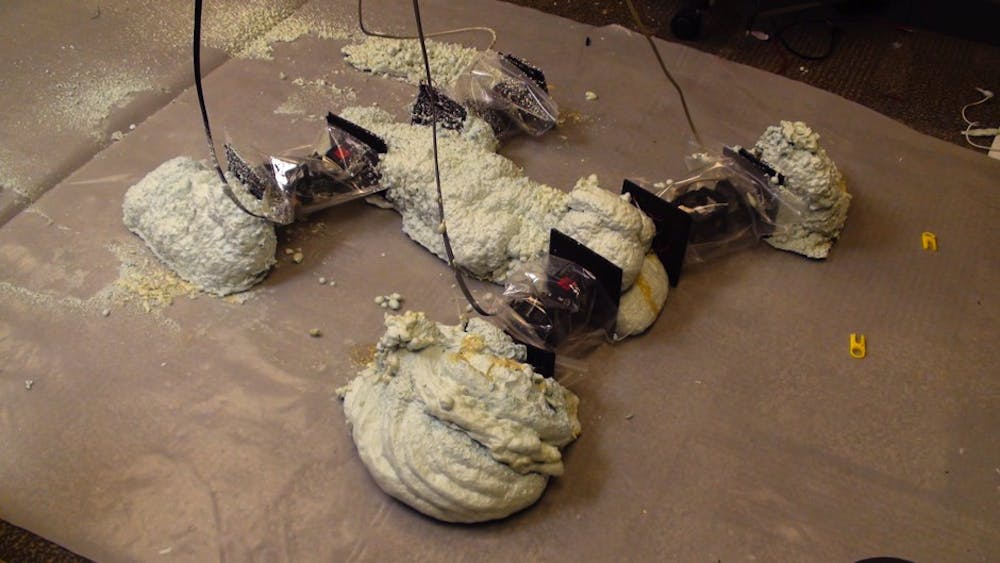
A group of scientists at Penn’s Modular Robotics Laboratory, or MODLAB, has built a robot that — in one sense — builds itself.
Their creation, the FoamBot, is the end-product of a set of smaller robots that are connected with layers of self-hardening foam. Lead researcher Shai Revzen believes the lab’s project will make robots even more relevant today.
“The reason we’re doing all of this is because we identified a problem in robotic missions,” said Revzen, who is also a postdoctoral research associate at the School of Engineering and Applied Science. He points to “unknown challenge missions” — any task where the robot doesn’t know what it needs to do until it gets to the scene — to demonstrate the FoamBot’s strengths.
“You land your rover on Mars and discover that the sample that could decide if there is life on Mars or not is on a cliff — and your robot can’t climb,” Revzen said. With the traditional one-function robot, “you’re stuck for 12 years, until the next launch” to send a new cliff-climbing robot back into space.
INTERACTIVE: How the FoamBot works
However, with the FoamBot, researchers can decide “post-facto” what kind of robot they want. “[You think], ‘Huh, I need to climb a cliff. How do I make a cliff-climbing robot out of the clusters I have?’ You figure out what kind of body you need and build the robot to this task,” Revzen said.
By “build,” Revzen means that a computer program can direct smaller “cluster robots” to particular positions and then order a foam-spraying robot to connect the clusters in a certain way. For example, a cliff-climbing robot might call for four cluster robots with foam feet, which can be raised by each robot, sprayed to the ends of each cluster.
Or, Revzen proposes, “[You just] landed your rescue people in Japan [and you realize you] need to crawl into this nuclear reactor. [You’re] going to need a snake-like robot,” which could be made out of four cluster robots lined all in a row and connected one after another with foam.
“Just [with] the addition of building passive mechanical body parts,” he said, “ we can greatly extend the possibility of robots to address unanticipated challenges.”
The FoamBot was inspired by Revzen’s observations of living organisms and the one key structure many animals have in common: a skeleton. “Skeletons are fundamental to how animals move. And if you want robots to move well, you need to create robot skeletons.”
He noticed that the Connector Kinetic roBots, small box-like robots which were created previously by MODLAB founder Mark Yim, were handicapped without a skeletal structure. “They have motors and a nervous system — microprocessors — but they don’t really have an equivalent of a skeleton or a body,” he said.
Although the current FoamBots don’t move as easily as a monkey or a kitten might, the concept promises great potential, he added.
“We demonstrated the concept in a way that … got the attention of many people of the robotics community, and we’re working on the next generation of the system. It will be able to build better robots … more practically,” he said. “Give it a few years [and] we might see viable robots.”
The Daily Pennsylvanian is an independent, student-run newspaper. Please consider making a donation to support the coverage that shapes the University. Your generosity ensures a future of strong journalism at Penn.
DonatePlease note All comments are eligible for publication in The Daily Pennsylvanian.